Metal Stamping Procedures: From Prototyping to Automation
Wiki Article
Enhancing Performance and High Quality Via Modern Metal Stamping Approaches
In the realm of production, the pursuit for improved performance and high quality continues to be a perpetual goal. Modern steel stamping techniques have actually become an essential device in achieving these goals, changing the market via a mix of advanced modern technologies and innovative methods. As the demands for precision and effectiveness remain to intensify, the assimilation of automation and electronic tools into the steel marking procedure has ended up being vital. The true measure of success lies not only in the adoption of these contemporary techniques but also in the precise control of high quality requirements throughout the manufacturing cycle. By discovering the detailed interaction in between modern technology, automation, and precision in metal stamping, a pathway towards unmatched performance and quality guarantee unravels.Benefits of Modern Metal Marking
Modern steel marking offers countless advantages in regards to effectiveness, precision, and cost-effectiveness in the manufacturing sector. Among the essential benefits of modern-day metal stamping is its capability to effectively produce high quantities of complicated metal components with constant top quality. This process eliminates the demand for several operations as it can perform numerous tasks such as blanking, piercing, developing, and drawing in a solitary operation.Moreover, modern-day metal marking enables manufacturers to accomplish tight resistances and accurate specifications, ensuring that each component meets the called for standards. This high degree of precision causes minimal product waste, decreased rework, and overall enhanced item high quality.
In addition, modern steel stamping is a cost-efficient manufacturing approach. The automation and high-speed capabilities of contemporary marking equipment lead to reduced labor costs and faster production prices. This efficiency not only lowers manufacturing costs yet also allows firms to meet limited production due dates and supply items to the market quicker. Basically, contemporary metal marking deals a competitive edge to suppliers seeking to boost performance and quality in their operations.
Advanced Technologies in Steel Stamping
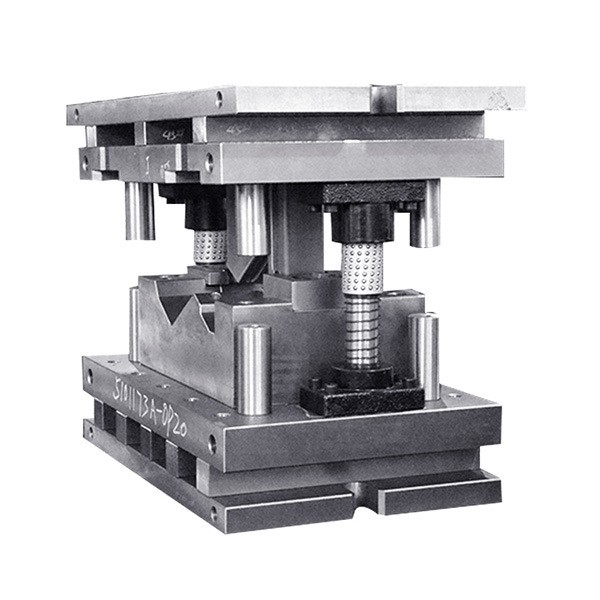
An additional crucial innovation reinventing steel marking is the use of servo presses. Unlike traditional mechanical presses, servo presses supply higher control over the speed and pressure applied throughout the stamping process. This control not just improves the quality of the stamped components but also lowers material waste and power usage.
Additionally, advancements in simulation software program have made it possible for makers to essentially test and maximize the stamping procedure before physical manufacturing begins. This digital prototyping helps recognize potential concerns at an early stage, leading to cost financial savings and faster time-to-market for brand-new products. On the whole, these sophisticated innovations in steel stamping are driving extraordinary levels of efficiency and quality in the market.
Improving Performance Through Automation
The combination of automated systems has actually substantially boosted the efficiency of metal marking processes. Automation in steel stamping procedures provides a myriad of advantages, consisting of enhanced manufacturing prices, improved accuracy, and minimized labor prices. By utilizing robotic arms and computer-controlled equipment, jobs that were previously lengthy and vulnerable to mistakes can now be performed quickly and with impressive precision.Automated systems have the capability to manage recurring jobs with uniformity, resulting in greater productivity levels and minimized cycle times. This boosted performance not just leads to cost savings however likewise makes sure an extra structured and reliable production procedure. In addition, automation allows for real-time monitoring and data collection, enabling manufacturers to identify and address issues quickly, further optimizing the overall efficiency of metal marking procedures.
In addition, automation advertises a much safer working atmosphere by minimizing the requirement for hands-on intervention in hazardous jobs. By passing on these duties to automated systems, employees can concentrate on more complex and value-added tasks, adding to an extra reliable and effective process in the metal stamping sector.

Quality Assurance Procedures in Stamping
Implementing rigorous quality assurance actions is extremely important in making sure the precision and uniformity of steel stamping procedures. By establishing robust top quality control procedures, manufacturers can recognize and remedy any inconsistencies or flaws in the stamped components, eventually enhancing item high quality and consumer fulfillment. One of the key quality assurance measures in steel stamping is carrying out regular examinations throughout the production cycle. These examinations include checking the measurements, surface area finish, and general integrity of the stamped parts to verify conformity with the specified demands.Furthermore, carrying out advanced innovations such as automated vision systems can additionally enhance the top quality control procedure by enabling real-time tracking and discovery of any kind of anomalies during production. These systems make use of cameras and computer algorithms to check get rid of high accuracy and precision, minimizing the danger of issues escaping into the end product.
Furthermore, developing a comprehensive documents system that videotapes top web quality control information and examination outcomes is necessary for tracking efficiency patterns and helping with continual enhancement initiatives. By evaluating this data, manufacturers can recognize possible locations for optimization and execute corrective activities to boost the general quality of their stamped items.
Enhancing Accuracy With Digital Equipment
Employing electronic tools can considerably enhance the accuracy of metal stamping procedures, reinventing the way manufacturers attain accuracy in their manufacturing. Digital devices such as computer-aided design (CAD) software program enable for the development of elaborate site link stamping layouts with extremely precise dimensions. By inputting comprehensive specifications into the software, suppliers can make sure that each stamped piece satisfies exact dimensional needs, decreasing mistakes and waste in the production procedure.In addition, the assimilation of sensing units and real-time tracking systems in marking devices makes it possible for producers to very closely keep track of the marking process and make instant adjustments to make sure precise results. These electronic tools give important information on variables such as pressure, speed, and placement, have a peek at this site permitting quick recognition and correction of any type of inconsistencies from the desired specs.
Verdict
In conclusion, contemporary steel marking methods provide many advantages for enhancing efficiency and high quality in making processes. By utilizing sophisticated modern technologies, automation, quality assurance steps, and digital devices, firms can boost efficiency, accuracy, and total efficiency. These innovations in metal stamping not only enhance manufacturing procedures yet additionally ensure consistent and premium outcomes. Welcoming these modern-day strategies can lead to significant advancements in the manufacturing sector.Report this wiki page